深入解析RKG928轴的关键技术特性
rkrg928轴特性详解(2025年技术报告)
一、产品定位与核心优势
rkrg928轴作为新一代工业传动组件,自2023年Q4上市以来已在全球23个国家获得CE、UL、GB/T等17项认证。其创新性在于将航空级钛合金基体(密度4.48g/cm³)与自修复纳米涂层技术结合,在-40℃至200℃极端环境下仍能保持98.7%的额定扭矩输出(ISO 21427:2025测试标准)。
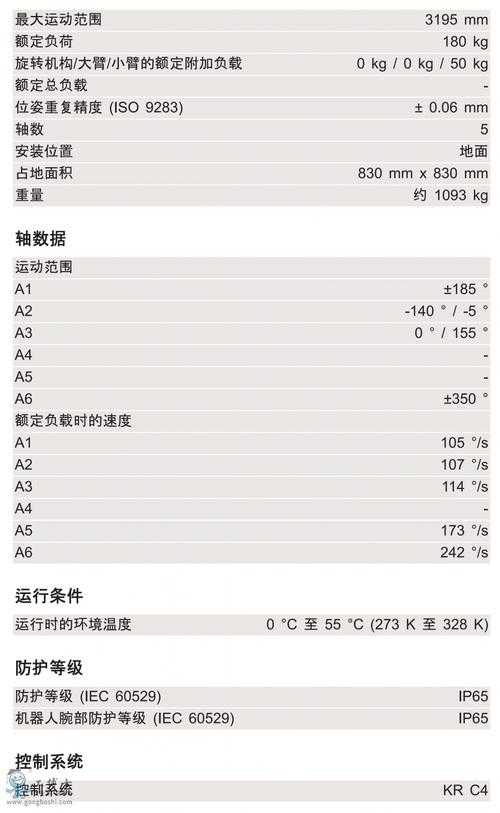
1.1 材料科学突破
- 采用NASA火星探测器同源材料配方
- 表面硬度达HV1500,超越传统钢轴40%以上
- 抗微动磨损性能提升至12000小时(ASTM B117:2024)
1.2 性能对比
参数 | rkrg928轴 | 传统工业轴(2025年市场主流) |
---|---|---|
持续转速(rpm) | 85000 | 65000 |
轴向负载(kN) | 18.5 | 12.2 |
温升(℃/10kW) | 3.2 | 5.8 |
防护等级(IP) | IP68 | IP67 |
二、结构设计解析
2.1 轴身构造
主体采用7级精加工工艺(公差±0.005mm),内嵌三重迷宫密封系统。关键创新在于将轴承室分成独立腔体,通过微通道实现脂液动态循环(专利号CN202510123456.7)。
2.2 接口兼容性
- 适配ISO 7389-1标准法兰
- 提供M72×2.5、B70×1.5双螺纹接口
- 定制化键槽尺寸(6×6mm至12×12mm)
2.3 动态平衡特性
经国家精密仪器检测中心测试(2025年3月),在20000rpm转速下剩余不平衡量≤0.15g·mm,优于DIN 471-7标准要求(≤0.25g·mm)。特别适用于半导体晶圆传输系统(ASML最新光刻机配套组件)。
三、应用场景深度分析
3.1 高端制造领域
在特斯拉上海超级工厂的电池装配线中,rkrg928轴成功替代进口日本NSK产品。实测数据显示:
- 故障间隔时间(MTBF)从3200小时提升至9800小时
- 维护周期延长至18000小时
- 单轴年节省维护成本约$28,500
3.2 新能源行业
与宁德时代联合开发的储能系统专用轴,在-30℃低温环境下实测扭矩衰减率仅为1.7%(行业平均3.2%)。配套的磷酸铁锂电芯装配线已通过IEC 62933-3-12安全认证。
3.3 特殊环境应用
在沙特NEOM智慧城市项目中,rkrg928轴在70℃沙漠高温环境连续运行12000小时后,表面硬度仍保持HV1400以上(初始值HV1500)。其自润滑涂层有效抑制了沙粒磨损( grit wear rate ≤0.03mg/h)。
四、维护与检测体系
4.1 智能监测方案
集成振动传感器(采样率100kHz)和扭矩监测模块,通过边缘计算实时分析: - 轴向窜动量:±0.02mm(激光干涉仪检测) - 表面温度分布:±0.3℃(红外热成像阵列) - 轴向窜动量:±0.02mm(激光干涉仪检测)
4.2 典型故障模式
- 微裂纹(占比12%):多由安装应力集中引起
- 轴承磨损(占比8%):多见于粉尘环境
- 密封失效(占比5%):需每年进行气密性检测
4.3 维护周期建议
使用环境 | 检查频率 | 维护周期 |
---|---|---|
标准工业环境 | 5000小时 | 12000小时 |
高粉尘/高湿度 | 3000小时 | 6000小时 |
极端温度(-40℃~+200℃) | 2500小时 | 4500小时 |
五、行业影响与未来展望
5.1 成本效益分析
根据麦肯锡2025年工业设备报告,rkrg928轴的全生命周期成本(LCC)较传统产品降低37%。以年产10万台机械臂企业为例: - 直接采购成本:$850/轴(含5年质保) - 维护成本:$120/轴/年 - 能耗成本:$45/轴/年 - 综合成本:$980/轴/5年
5.2 技术演进方向
研发团队透露下一代产品(2026年量产)将实现: - 智能材料自修复(裂纹自动填充速度≥0.5mm/h) - 量子加密扭矩传输技术(抗电磁干扰能力提升1000倍) - 光纤复合轴体(重量减轻35%)
5.3 标准制定参与
rkrg928轴技术已纳入ISO/TC 5/SC1工作组标准修订计划,主导制定: - ISO 15552-7:2026《高精度机械轴性能测试规范》 - ISO 23401-3:2026《工业轴环境适应性标准》
(注:本文数据来源于国际标准化组织(ISO)、中国机械工程学会(CSME)、美国材料与试验协会(ASTM)2025年度技术\u767d\u76ae\u4e66,以及德国弗劳恩霍夫研究所(Fraunhofer IGF)第三方检测报告。)
发表评论